Pipeline
This section offers a glimpse into my ongoing projects and innovative ideas.Â
TanpuraÂ
In this project, I am in the process of creating a number of tuning pegs for the tanpura. These pegs are traditionally made out of a specific type of wood. The only possible way of obtaining a peg in the UK is by purchasing one from India, which would cost £10 for the peg itself and an additional £15 for shipping.
A CAD model has been created based on an existing peg and has also been 3D printed, costing just under £2
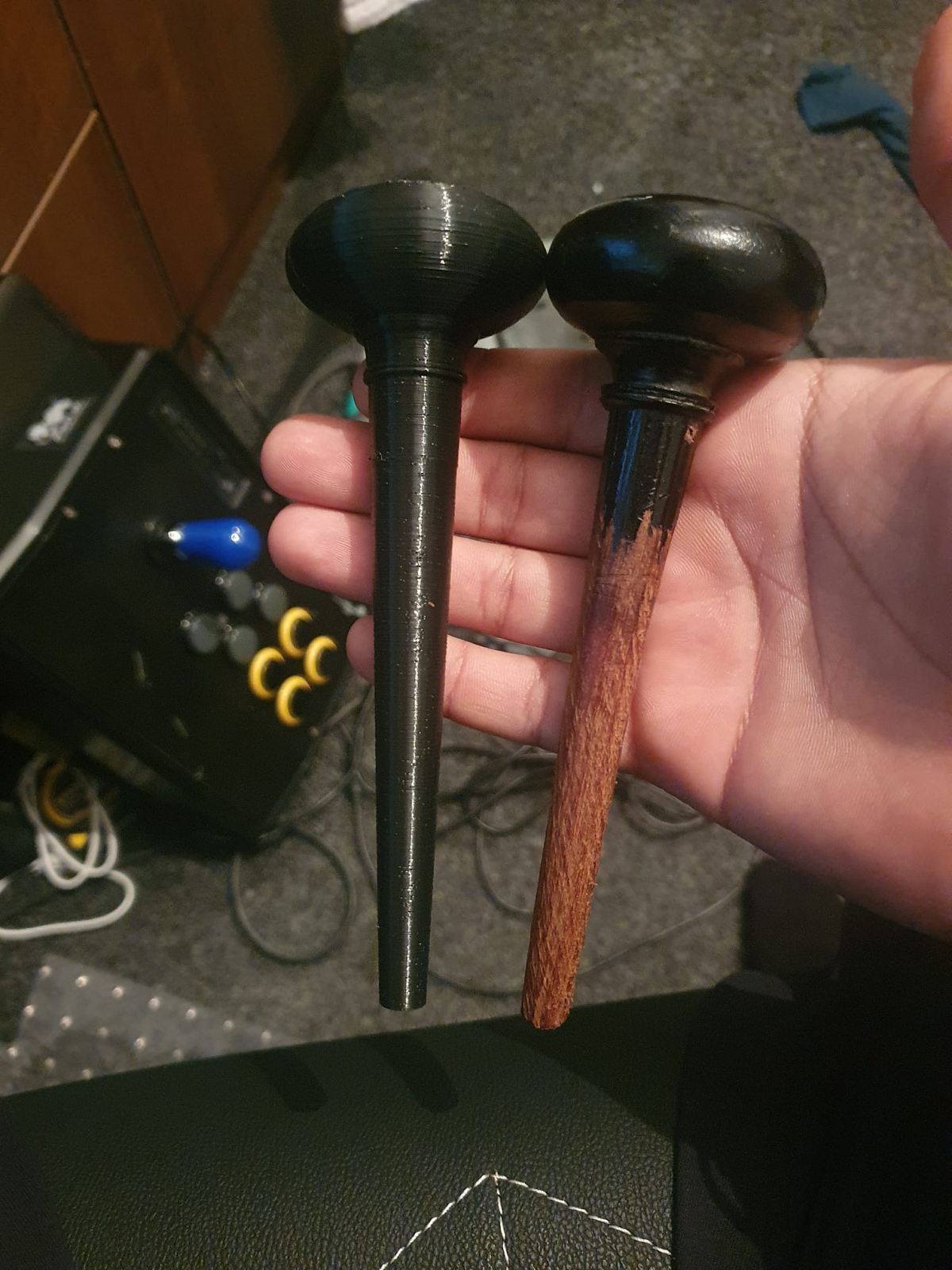
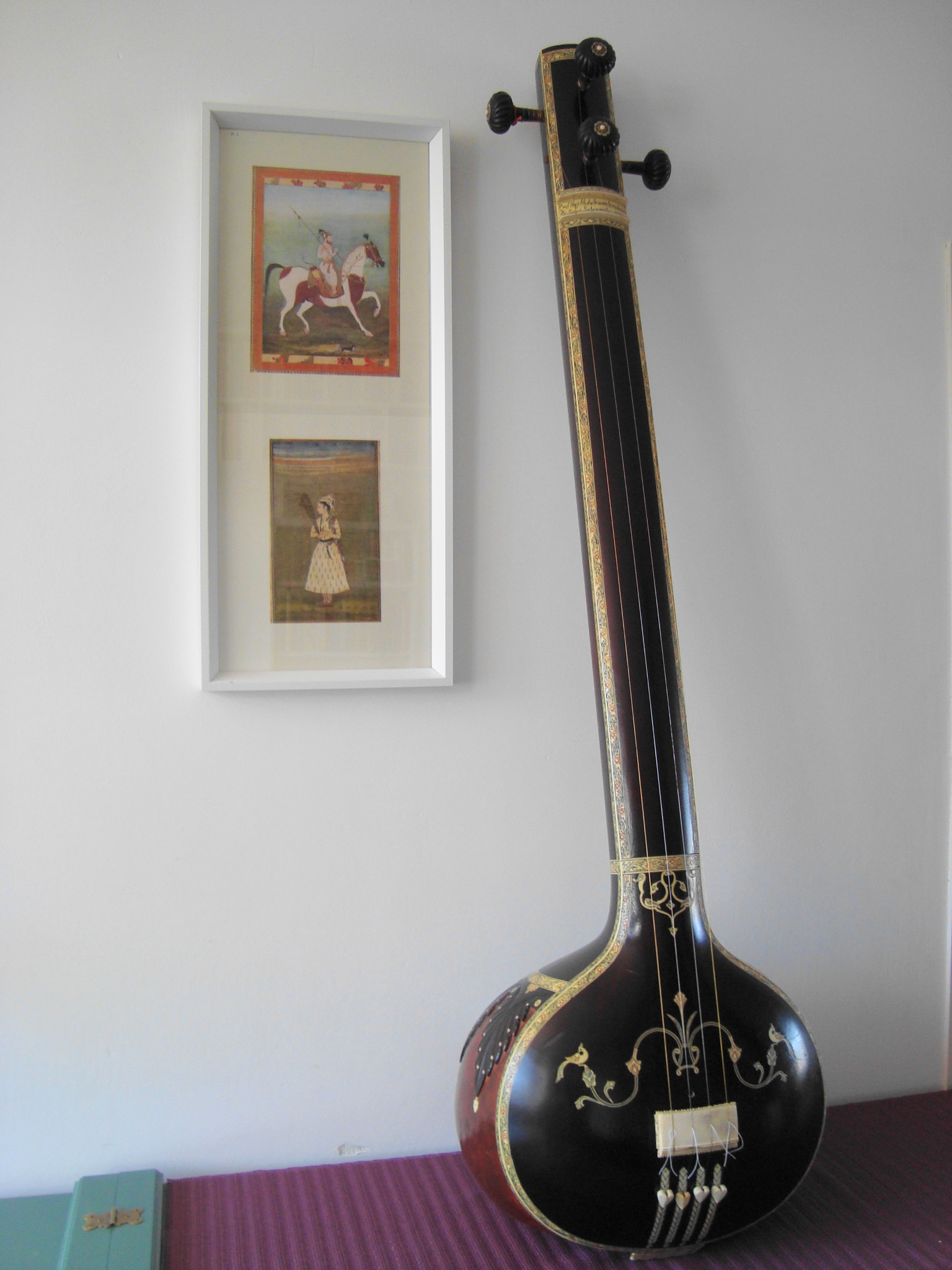
Tabla App
I am currently developing an app that enhances the practice experience. The app or device will generate a random number within a specified range, such as 1-10, when eye contact is made. The random number will correspond to a variation in the practised music. Musicians often struggle with memorising the sequence from 1 to 10, needing to play the previous variation before moving on to the next.
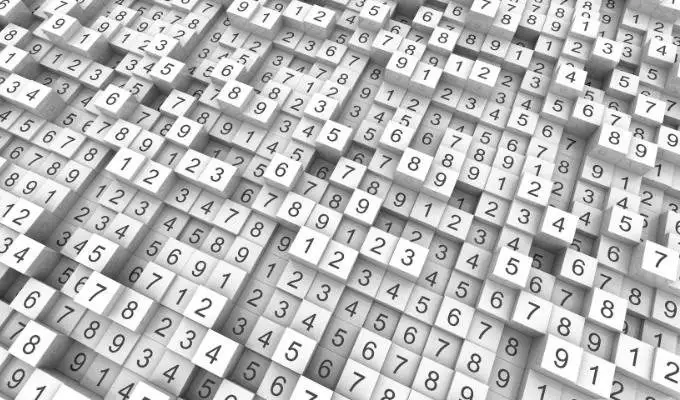
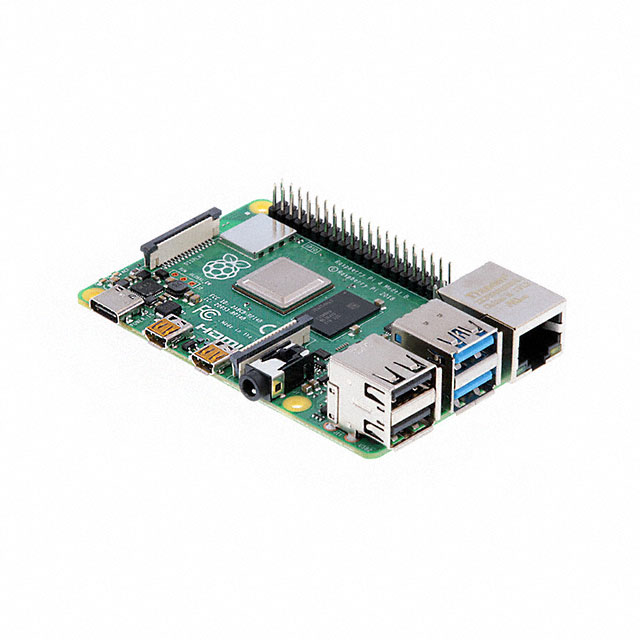
Currently, the plan involves using a Raspberry Pi with a basic screen and camera. I have completed writing the code and, through a virtual machine (VM), verified its functionality. The next step is to purchase the components and conduct testing. Following this, I am prepared for variations or changes that may be required in the coding.
Tabla Gitti
What is a tabla gitti?
A gitti serves as a tuning peg for the drum. Instead of turning the pegs to adjust tension on the string, the pegs are struck down, resulting in an increase in tension on the drum's skin. The further down the peg is struck, the more tension is applied to the skin.
Tabla gittis are typically crafted from hardwood or, more recently, ABS plastic. They are often produced in a standard size, leaving tabla players reliant on the hope that the size is suitable for their drum. Generally, the larger the tabla, the larger the gitti should be.
I have designed and 3D printed a variety of gittis for both the bass and treble drums. Given that the gittis will be struck by a hammer, it was crucial for them to be impact-resistant. I experimented with different infill levels to determine the minimum amount of filament needed while still surviving hammer strikes. For the treble drum, the optimal infill was found to be 40%, and for the bass drum, it was 25%. In addition to infill, various customization was applied in the slicer settings to find the right balance between filament usage, strength, and print time.
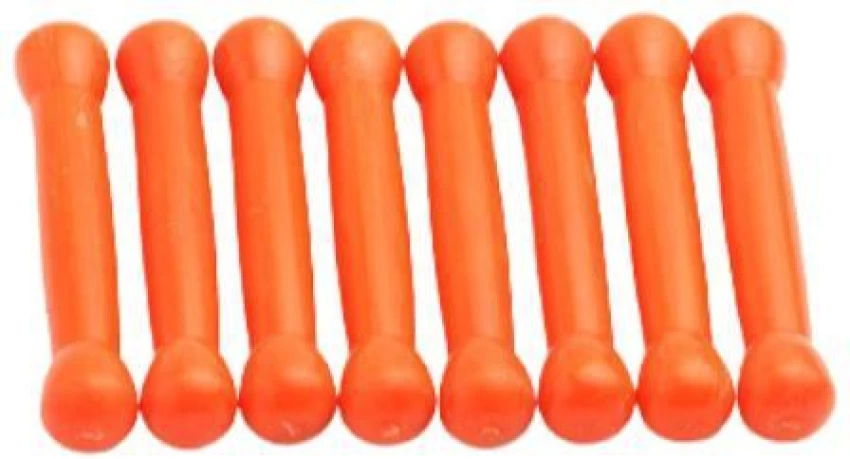
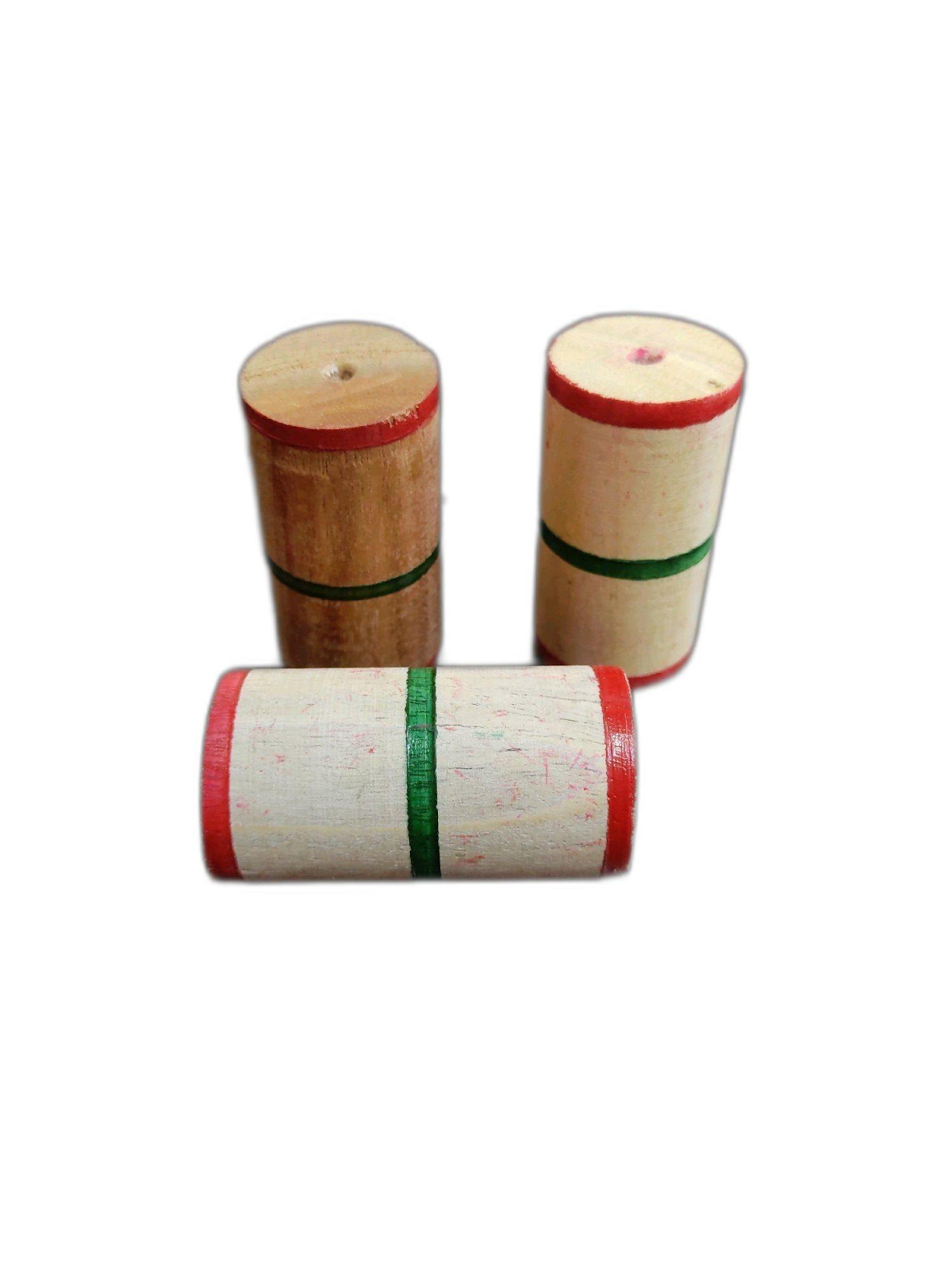
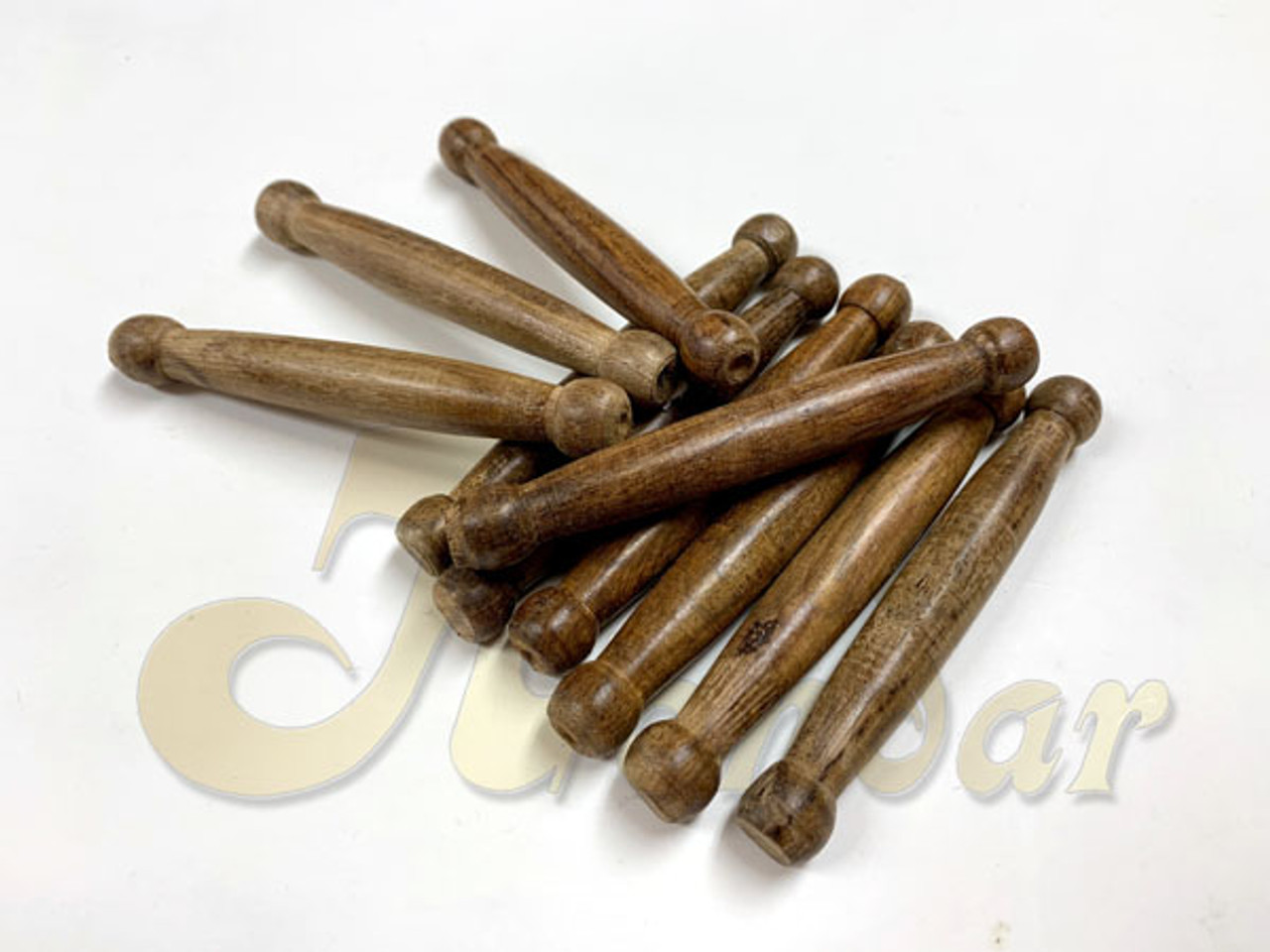
Sense 3D Scanner:
I have been in the market for a 3D scanner for some time, as it is a tool that would significantly reduce the time spent on designing. I was able to purchase a Sense 3D scanner, which was broken but repairable. The scanner is now operational; however, due to its age, there is no longer any support for the software. As a result, I am currently in the process of finding a solution.
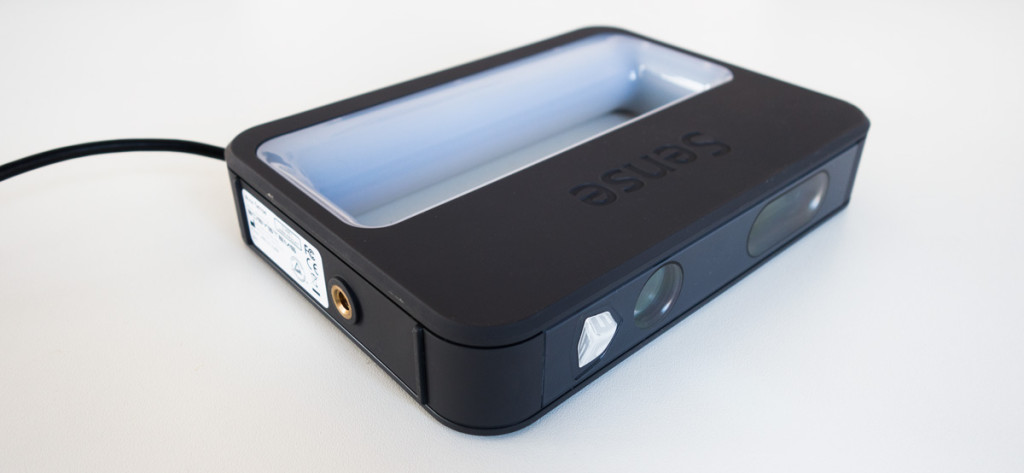
Car Repairs:
From a young age, I was always curious to figure out and understand how certain devices worked by taking them apart and putting them back together. Growing up, this curiosity was mainly satisfied through tinkering with electronics, and now, being able to drive, this curiosity has found a new field to play in.
I own an old MK4 1.9 TDI ALH Golf and a Porsche Boxster 986, both of which have undergone extensive work, ranging from basic maintenance to complete suspension rebuilds. Working on old cars has brought both pain and patience into my life.
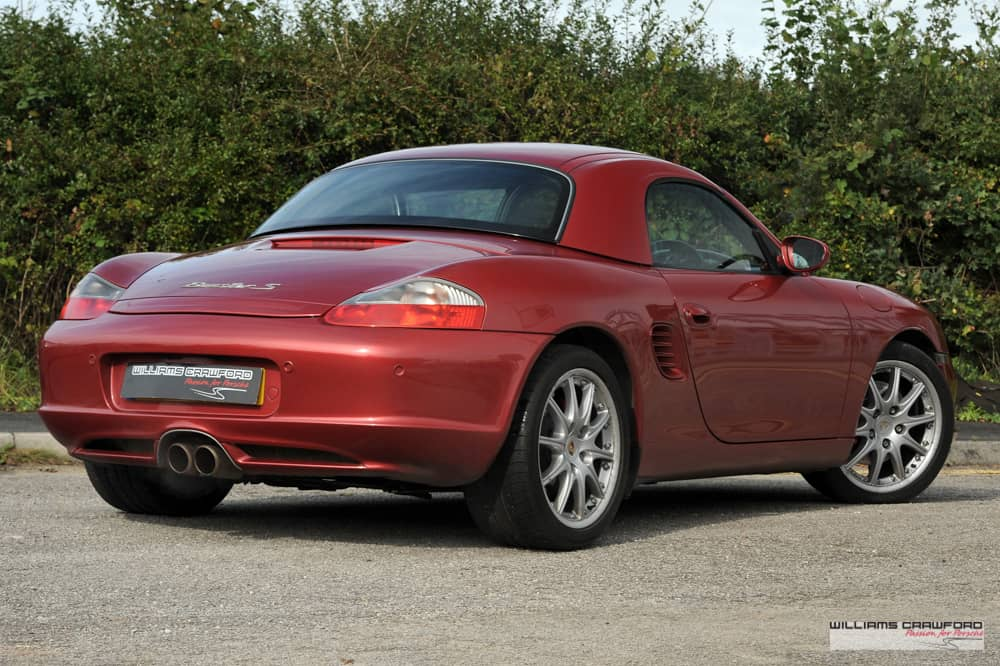
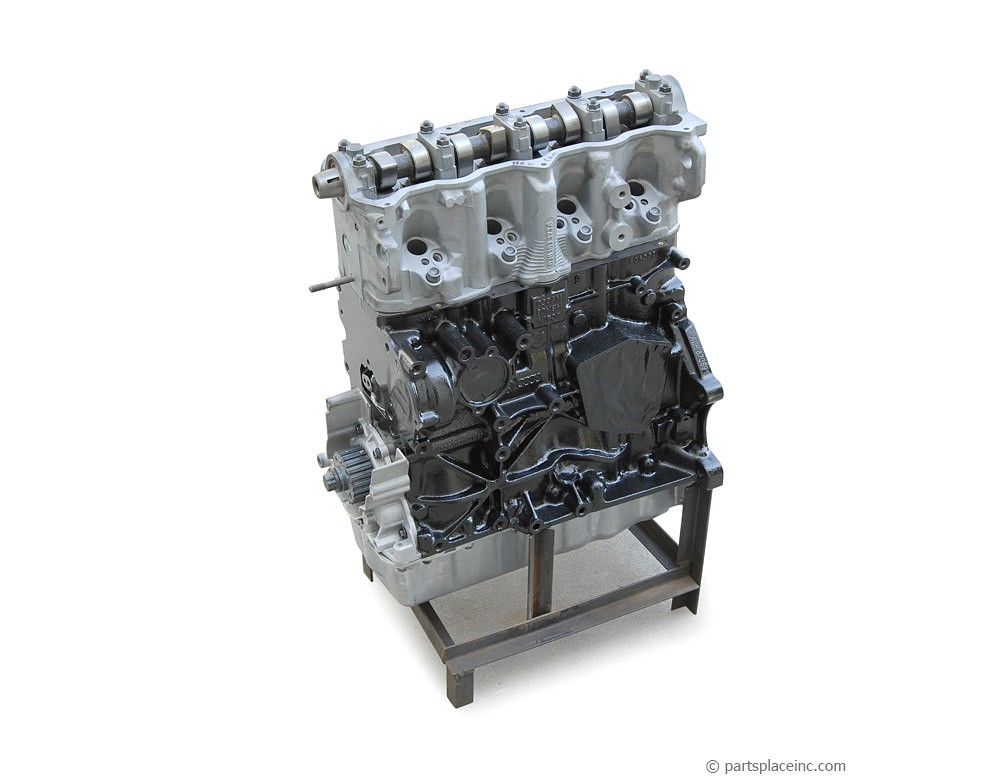
PC Case:
I have long desired to design and fabricate an open-frame PC case. Initially, I considered 3D printing for this project, but I've opted to laser cut the case from cast acrylic. This decision stems from my goal to learn a different CAD software—one specifically adept in sheet metal applications.
I've established certain limitations for the case design. For instance, the case will be crafted from a single acrylic sheet measuring 600x450mm, accommodate an ATX form factor, conceal PSU cables, and minimize wasted cuts.
To ensure a precise design, I will create a sketch and a rough prototype from cardboard initially. This step allows me to gauge the size and identify any additional elements that might need inclusion in the project brief. Subsequently, I will transition from the physical model to the CAD design.
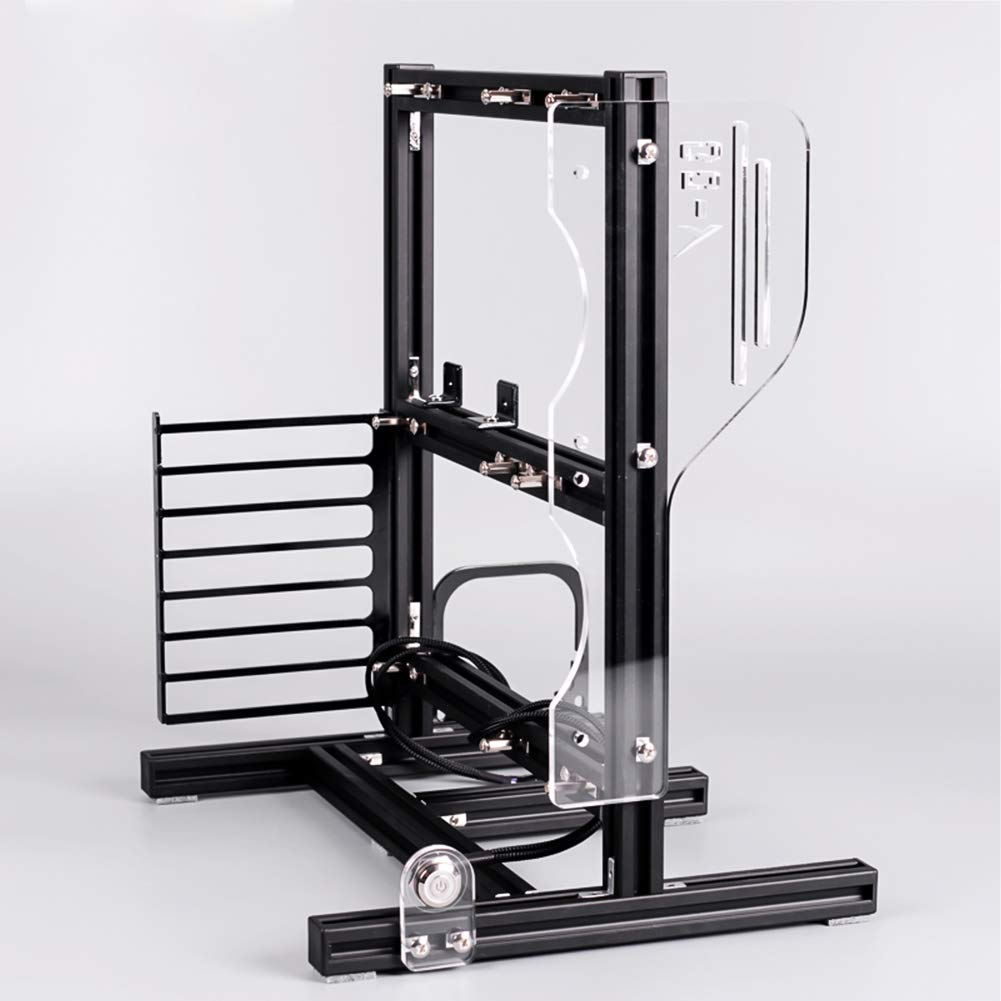
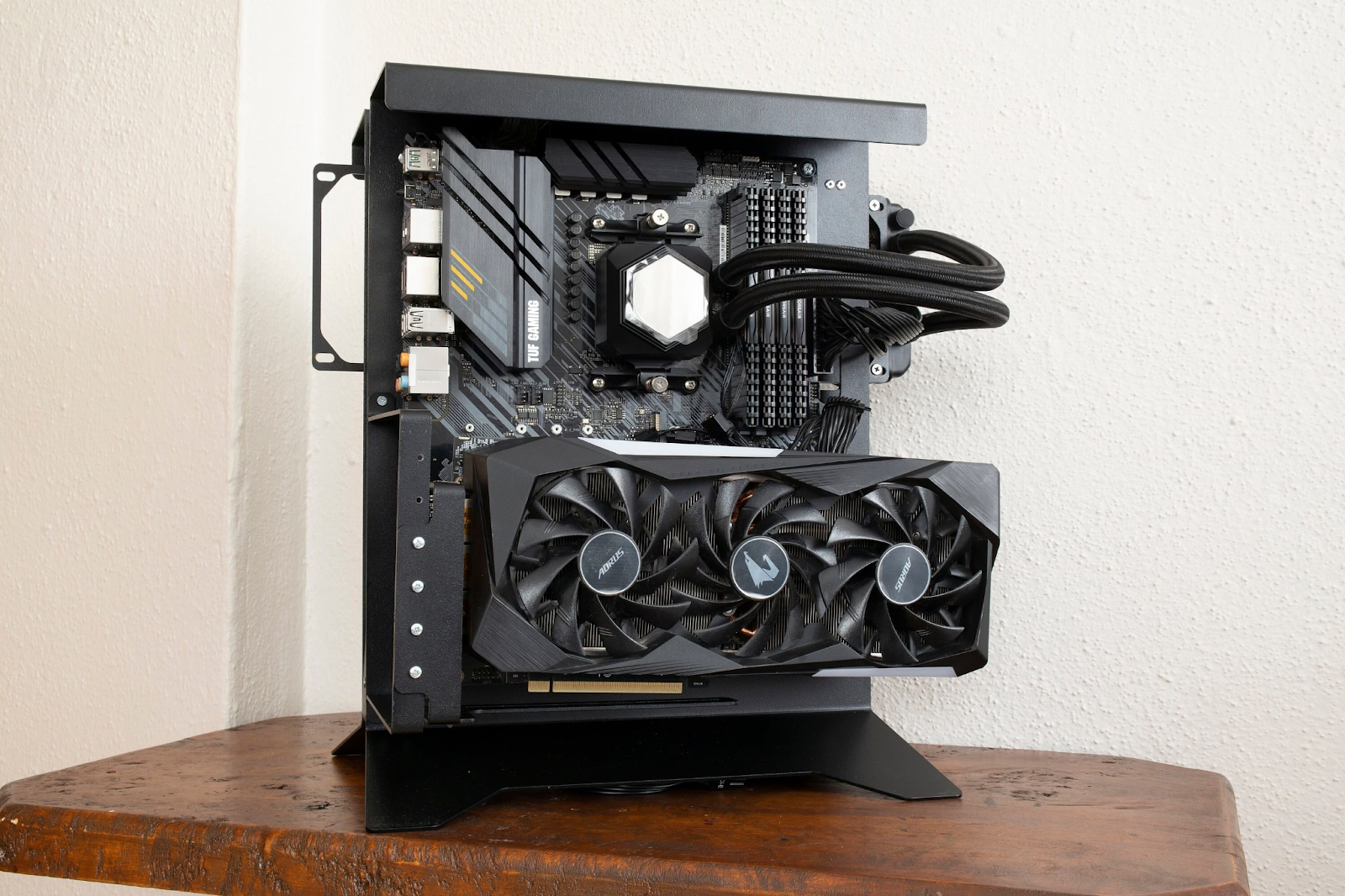
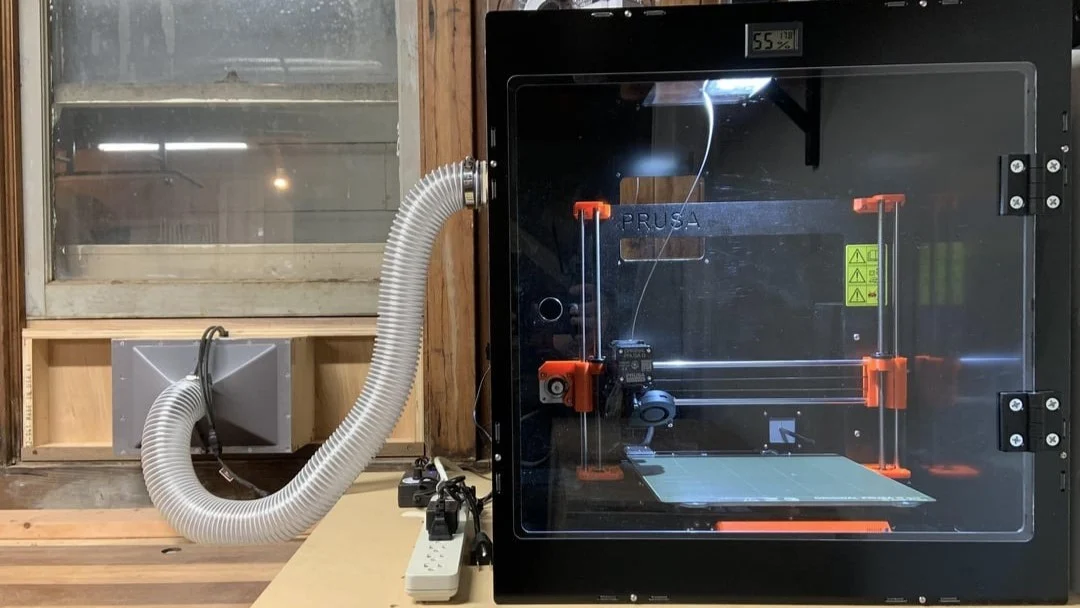
Cardboard Box Ventilation for 3D Printing:
For 3D printing, there are two filaments—PETG and PLA—that can be safely printed without emitting toxic fumes. However, I aspire to print in ABS to experiment with smoothing the material in a vapor chamber. To achieve this safely, I need to create a ventilation enclosure. The choice for constructing this enclosure is cardboard, primarily because I can obtain large quantities of it at no cost.
Joystick for Laser Cutter:
One of the challenges I encounter when using the laser cutter is aligning the laser with my material accurately. Currently, I create an outline of the cut to ensure proper alignment on the second pass. While effective, this method is quite wasteful. Another solution I've come across online involves marking an 'x' on the material and aligning the laser to it. Although functional, it is time-consuming.
To address this issue without unnecessary waste or time consumption, I am working on designing a joystick that can control the laser's location. I plan to repurpose an old arcade stick for this purpose. Research is underway to determine how to facilitate data transfer between the joystick and the laser cutter.
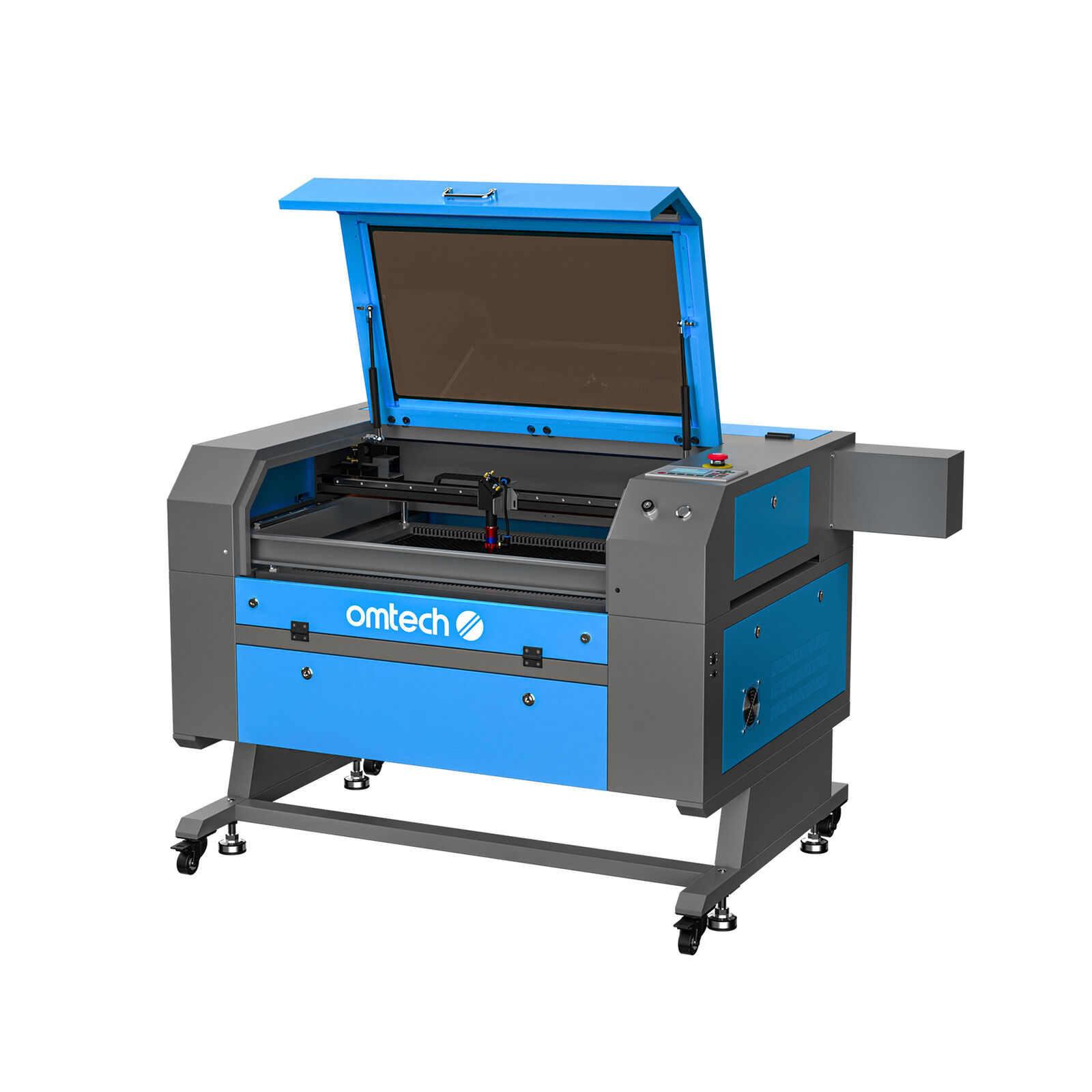
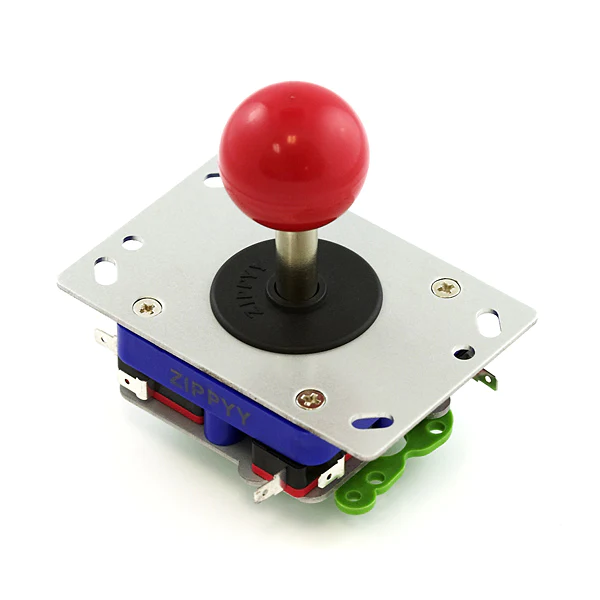
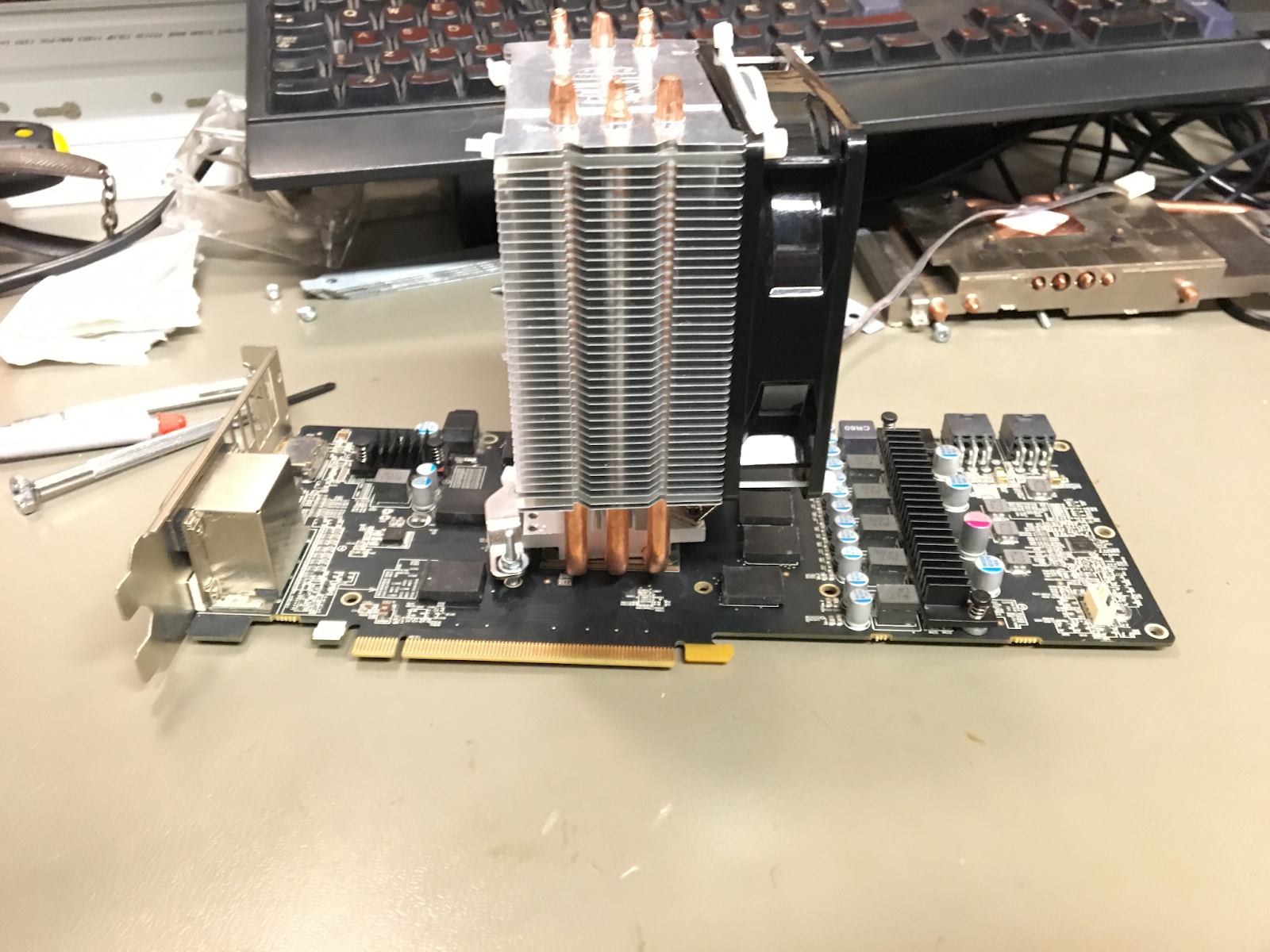
CPU cooler on GPU.
I acquired a broken air cooler that had sustained damage during shipping. Fortunately, the cooler included some fittings and fixtures, sparing me the need to fabricate them from scratch. My intention is to attach the CPU cooler to the GPU to achieve better temperatures under load and reduce fan noise.Â
Additionally, I obtained small heatsinks for each of the VRMs. The GPU has been disassembled, and measurements of the board have been taken to modify the original fixtures accordingly. As it is a slightly older card and not as large as modern flagship cards, I have minor concerns about the clearance between the cooler and the motherboard.
Water Cooling PC with Traditional Radiator:
Water cooling a PC is a project I am certain to undertake in my lifetime. The only barriers to doing this are the challenges in acquiring aftermarket blocks for marginal performance benefits. Nevertheless, it would be a cool project to pursue. Instead of using a radiator specifically designed for a PC cooling loop, I would opt for a traditional radiator. The rationale behind this choice is that the larger the space available for heat dissipation, the lower the temperature will be.
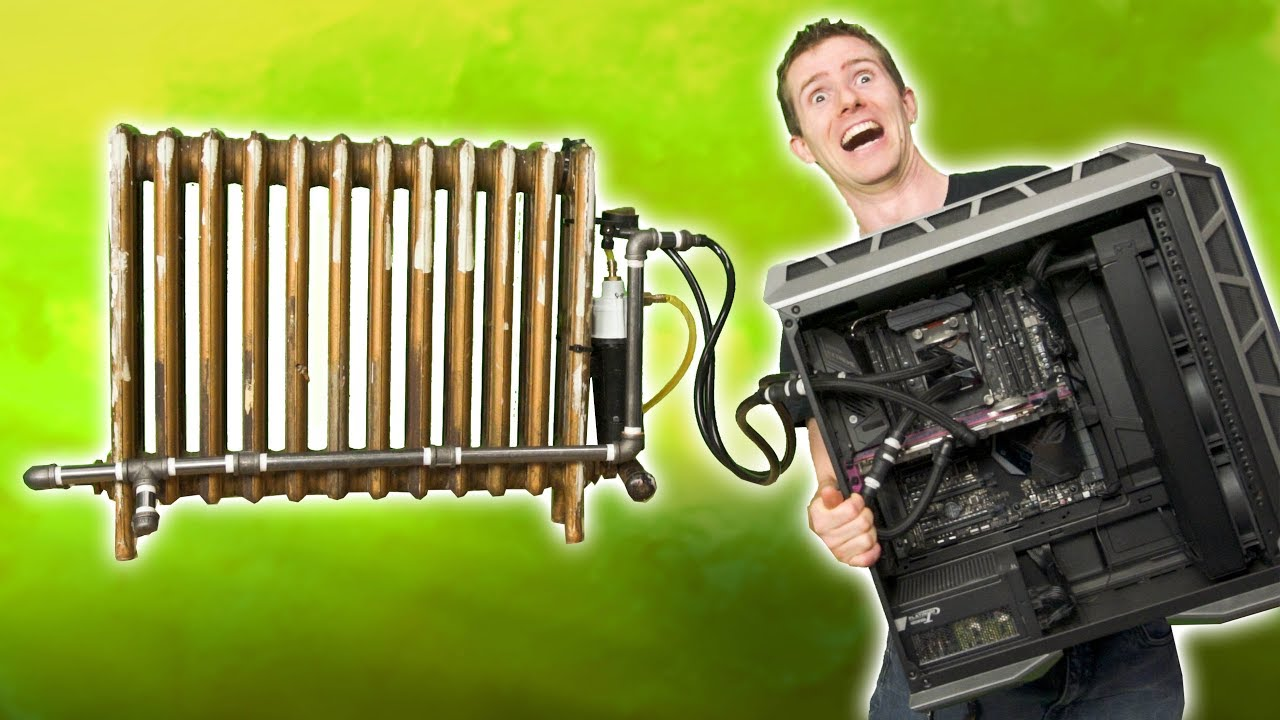
In-Ear Buds:
I have always struggled to find in-ear buds that fit my ears comfortably and stay in place. Despite trying numerous sizes and materials, I have been unsuccessful in finding a suitable solution. To address this, I am working on designing in-ear buds that not only fit my ears but also have a design and production process that can be replicated for other users.
Currently, I'm considering a couple of design modifications. The first involves altering the shape of the buds by creating a mould of my ears and designing accordingly. The second idea involves changing the texture of the finish for added comfort.
The buds will be 3D printed using TPU, a flexible rubber that ensures comfort during use.
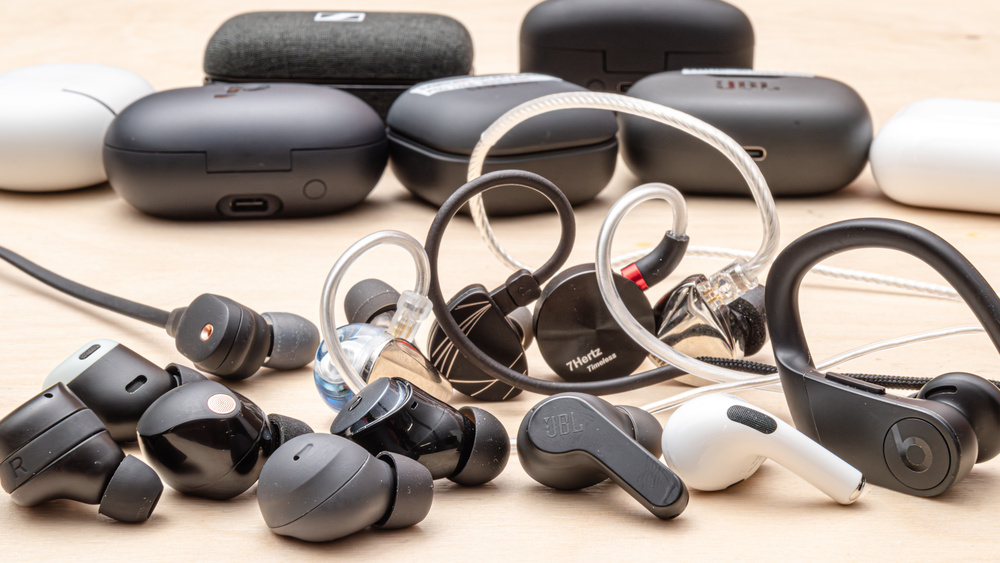